Front suspension design
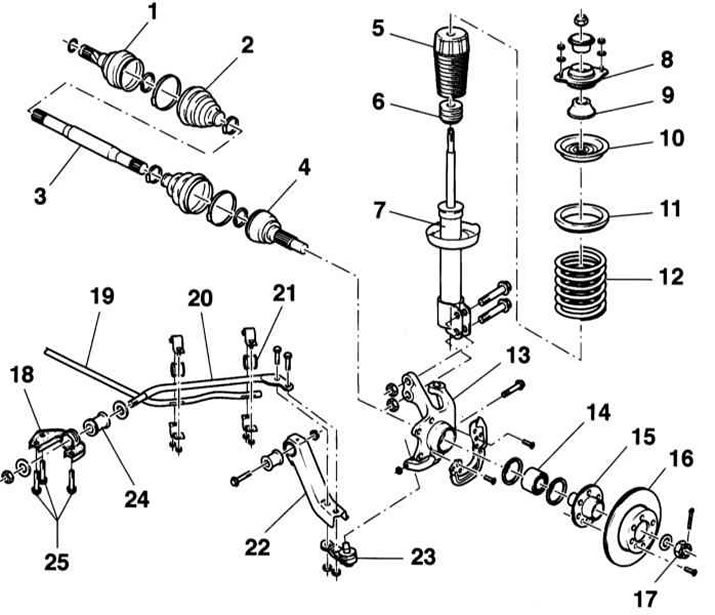
1 - Inner CV joint
On engines DOHC 1.0 and 1.2 l:
Tripod hinge.
2 - Cover of the inner CV joint
3 - Drive shaft
4 - Outer CV joint
5 — Case
6 - Buffer stroke compression
7 - Shock absorber
8 - Thrust bearing
9 - Spacer
10 — the Top cup of a spring
11 - Damping ring
12 - Spring
13 - Swivel fist
14 - Wheel bearing
15 - Wheel hub
16 - Brake disc
17 - Castellated hub nut
18 - Rod holder
19 - Anti-roll bar
20 - Thrust
21 - Rubber support
22 - Wishbone suspension
23 - Ball joint
24 - Damping sleeve
25 — Bolts with shoulder
The Opel Corsa and Tigra are equipped with a linkage rear suspension with link beam. The suspension consists of an open transverse tube to which a trailing arm is welded on each side. An additional stabilizer is located in the transverse pipe. Trailing arms are bolted to the body through rubber-metal bearings. Coil springs and hydraulic shock absorbers are used to reduce the feeling of bumps in the road. The rear wheel bearings are adjustable. The Combo model has a rigid axle with leaf springs and shock absorbers, which are characterized by high strength. This design provides the possibility of significantly greater loading of the car. Compared to models Corsa B and Tigra the design of the rear wheel bearings has also been changed. They are not built into the brake drums, but are located in a separate hub, bolted to the brake drum.
Rear suspension design for Corsa and Tigra models
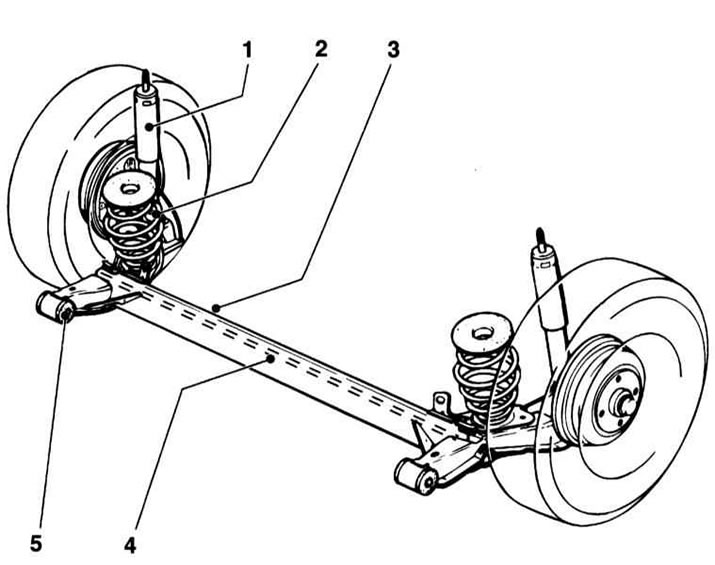
1 - Shock absorber
2 - Helical spring
3 - Connecting beam
4 - Anti-roll bar
5 - damping sleeve
Rear suspension design of Combo models
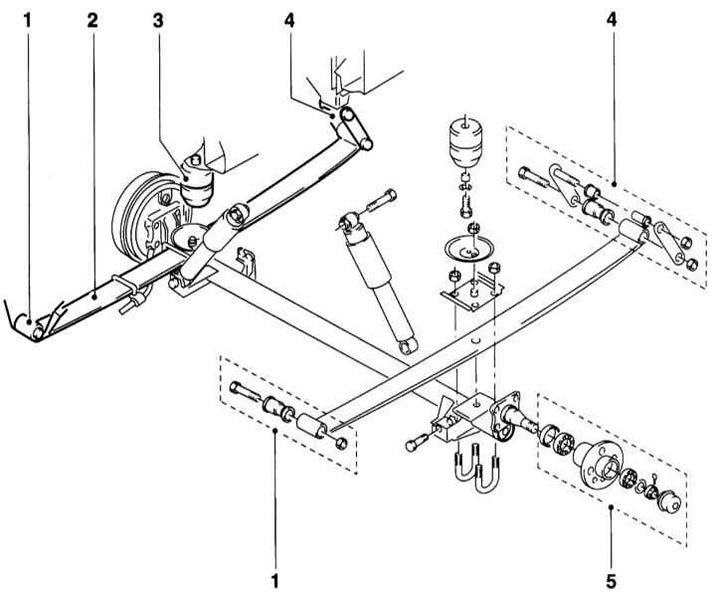
1 - Front spring mount
2 - Spring
3 - Additional spring
4 - Rear spring mount
5 - Assembly of the wheel hub
Since 09.1997, the design of the wheel bearing hub cap has been changed on Combo models.
The steering gear consists of a steering wheel, a steering shaft and steering rods. The steering wheel is fixed to the steering shaft, which is connected to the steering mechanism. Through the rack and pinion, the rotation of the steering shaft is transmitted to the rack. The toothed rack is connected to the steering rods through ball joints. The latter, through the hinges and steering knuckles, transmit movement to the front wheels of the car. The steering gear must be easy to move and must not have play. It does not require maintenance, but during the period of maintenance it is necessary to check the tightness of the sealing collars. Depending on the model and equipment of the car, it can be equipped with power steering (power steering). Vehicles with engines DOHC 1.0 and 1.2 L equipped with electric power steering (EPS); on cars with OHC engines from 1.2 to 1.7 liters conventional power steering is used. The task of the power steering is to reduce the effort required to turn the steering wheel, especially at low speeds or when parked.
Steering column design
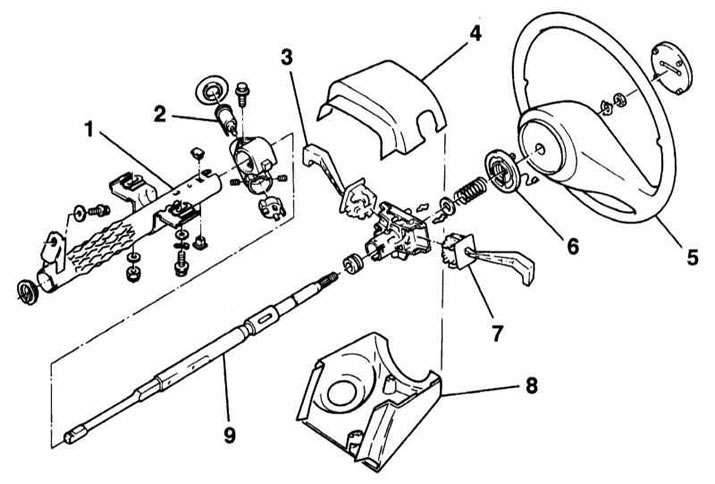
1 — a casing of a steering column
2 — the Cylinder of the lock of ignition
3 — the Steering column switch of screen wipers
4 — the Top overlay of a steering column
5 - Steering wheel
6 - Cable drum
7 - Steering column switch for outdoor lighting
8 — the Lower overlay of a steering column
9 - Steering shaft
The design of the steering gear without power steering
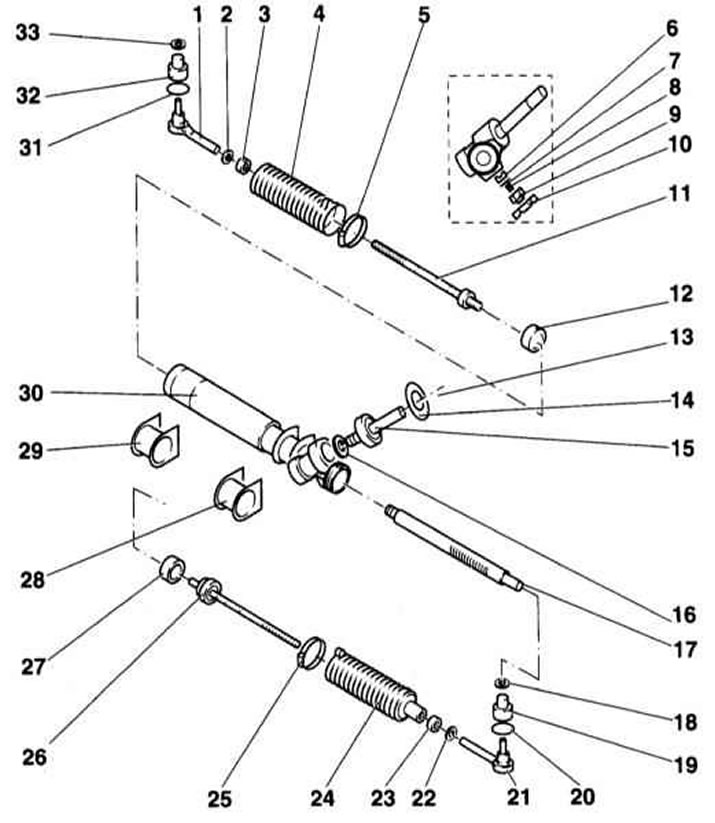
1 - Tie rod end
2 - Locknut
3 - Clamp of the protective casing
4 - Protective cover
5 — a collar of a protective casing
6 - Support-pressure element
7 - O-ring
8 - Spring
9 - Adjusting plug
10 - Lock nut
11 - Tie rod
12 - Thrust ring
13 - O-ring
14 — Retaining ring
15 - Gear with bearing
16 - Guide sleeve
17 - Gear rack
8 - Lock nut
19 - duster
20 — Retaining ring
21 - Tie rod end
22 - Locknut
23 - Clamp of the protective cover
24 - Protective cover
25 - Clamp of the protective cover
26 - Tie rod
27 - Thrust ring
28 - Left rubber support
29 - Right rubber support
30 — the Case of the steering mechanism
31 - Retaining ring
32 - duster
33 - Lock nut
The power steering consists of a pump, a power steering fluid reservoir and connecting hoses. The pump is driven by the engine via a V-belt. The pump delivers fluid from a high pressure reservoir to a valve body located in the steering gear. The valve is connected to the steering shaft and supplies oil, depending on the direction of rotation of the steering wheel, to the corresponding side of the power steering cylinder. The fluid acts on the piston and thus makes it easier to turn the wheels. At the same time, the piston forces fluid from the other side of the working cylinder through the hydraulic return line into the reservoir.
The principle of operation of EPS is as follows. Steering wheel rotation is detected by a torque sensor (3), the signal is sent to the EPS control unit (5). From the VSS and the ECM, the EPS control unit receives information about the vehicle's speed. The EPS control unit calculates the required amount of force generated by the electric motor (1) and transmits to the steering mechanism (8). The amount and direction of the assist force is determined by the amount of motor current determined by the EPS control unit. Through the lower steering shaft (7) there is a direct mechanical connection between the steering wheel and the steering mechanism. Thus, if the EPS fails, the vehicle remains steerable. EPS only works when the engine is running.
Power steering design (DOHC 1.0 and 1.2 L models)
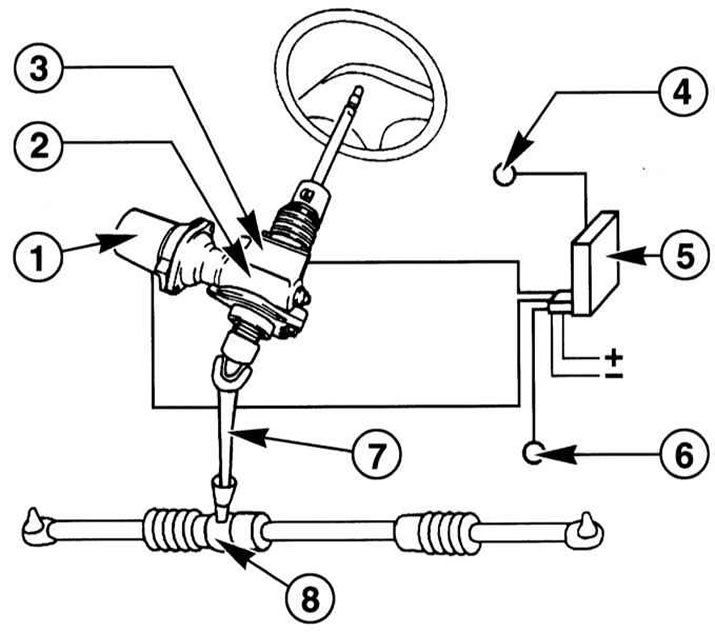
1 - Electric motor
2 - Worm gear
3 - Torque sensor
4 - Signal from VSS
5 - EPS control unit
6 - Signal of the number of revolutions of the crankshaft from the ECM
7 - Lower steering shaft
8 - Steering gear
Often, during the maintenance of suspension components, one has to deal with hard-to-return fasteners. «sticking» fasteners due to the fact that they are constantly exposed to external influences, are in contact with water, dirt, soot and other substances that contribute to the development of corrosion. In order to facilitate the procedure for giving such «stuck» fasteners, it should be impregnated in advance with a copious amount of penetrating oil. Scouring exposed threaded parts of fasteners with a stiff wire brush also helps loosen rusted nuts. Sometimes, in especially severe cases, for letting go «stuck» bolts / nuts, you can use a drift. The punch rests against the edge of the slot of the nut / bolt head, then sharp blows are applied to its opposite end with a hammer. Make sure that the drift does not break, try not to damage the thread with inaccurate blows. Heating a non-retractable fastener and the surrounding surface of the component with a blowtorch or gas burner is also a fairly effective method, although the drafters of this Guide do not recommend resorting to this technology unless absolutely necessary due to its potential danger associated with the possibility of fire and the risk of burns. To increase the torque when releasing fasteners, various kinds of extensions, gates and pipe nozzles are used on them. However, remember that you should not use this kind of amplifying devices complete with equipped «ratchet» drive - the risk of failure of the ratchet mechanism is too great. Sometimes a nut/bolt starts to give in after it has been pre-tightened slightly in a clockwise direction. All fasteners, the release of which required the use of extraordinary measures during assembly, must be replaced!
After giving away, carefully check the condition of the fastener and, if necessary, replace it with elements of the same size. When assembling, tighten the fasteners of the suspension and steering components strictly with the required force.
Never attempt to straighten deformed suspension and steering components - replace defective parts with new ones!
Since the maintenance procedures for the suspension components are performed under the vehicle, care should be taken in advance to raise the vehicle and fix it in a raised position (prepare a reliable jack and props).
Under no circumstances should you carry out any work under the vehicle, which has only been secured in the raised position with a jack!
Precautionary measures
An airbag is built into the hub of the steering wheel. To ensure that the airbag deploys properly in a crash, and to avoid the risk of injury from accidental airbag deployment, certain precautions must be taken (see also Chapter Onboard electrical equipment):
- Before starting work on the airbag, or near the SRS wiring route, be sure to disconnect the negative battery cable, start work at least one minute after disconnecting the battery, - time is needed to discharge the reserve power supply capacitor;
- Do not allow the airbag module to exceed 90°C. Do not turn the removed airbag module upside down;
- Do not allow solvents and detergents to get on the surface of the module - use only a clean, slightly damp cloth to wipe the steering wheel;
- The SRS control unit and airbag modules are sensitive to directional overloads (blows) and after a fall from a height of more than 50 cm must be replaced;
- Before carrying out welding work on the vehicle, be sure to disconnect the electrical wiring of the SRS control unit;
- On models equipped with passenger airbags, to avoid injury, do not install any accessories or place any foreign objects in the airbag deployment area.
Visitor comments