Note. To prevent damage to the thrust plate spring petals, use the KM 6263 special tool when removing and installing.
Note. Pay attention to the different lengths of the brackets for attaching KM 6263 when lowering the engine block.
Removing
Remove the gearbox.
Note. Special tool KM 6263 can only be attached to the engine block and not to the oil pan.
Attach special tool KM 6263 to the engine block and tighten 4 bolts (arrows in the picture).
Note. Do not overtighten the bolts.
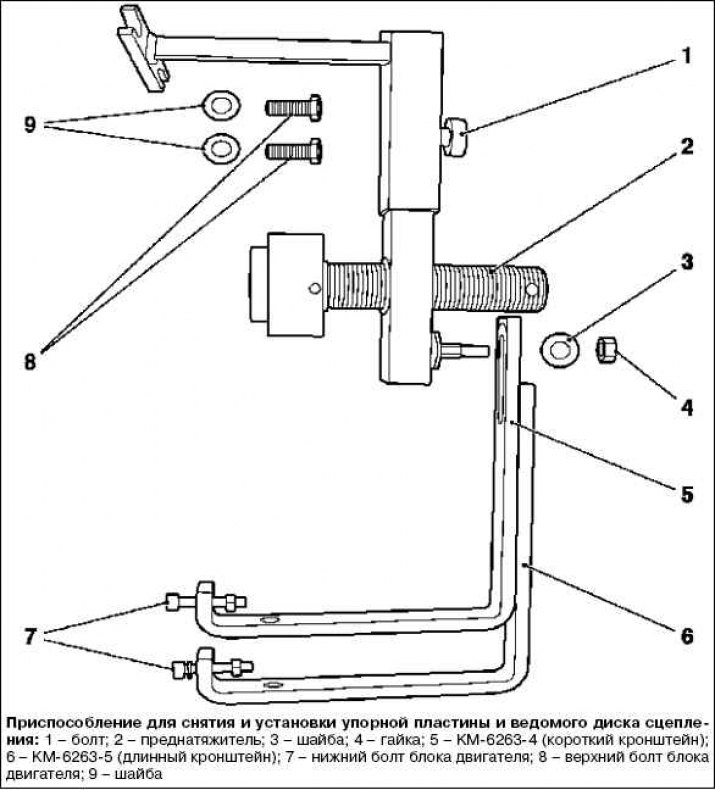
Attach special tool KM-6263-30 (4) to the center mandrel.
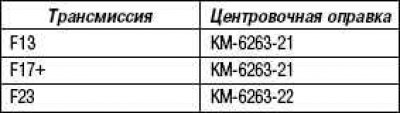
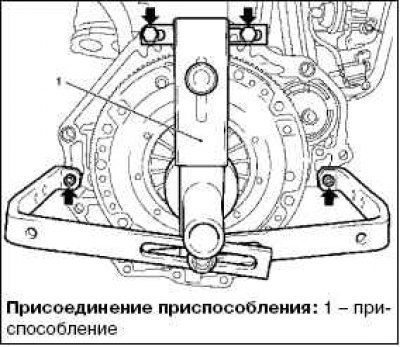
Fasten the special tool KM 6263.
Align the KM 6263 special tool with the center.
Install the centering mandrel with special tool KM-6263-30 through KM 6263 into the clutch disc and crankshaft (center).
Tighten the bolt and nut.
Tighten 4 bolts of special tool KM 6263 on the engine block.
Release the clutch disc.
Install the KM 6263 special tool so that it is opposite the thrust plate spring tabs.
Turn the special tool KM 6263 clockwise to the stop.
Remove thrust plate from flywheel.
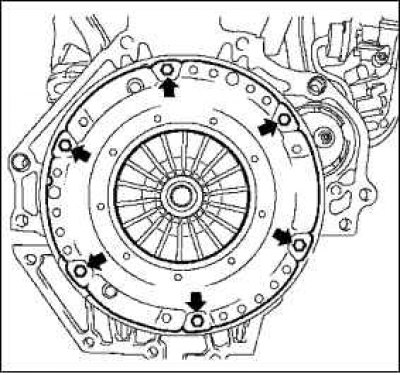
Loosen 6 mounting bolts (arrows in the picture).
Note. The figure shows the clutch without special tool KM 6263 and centering mandrel.
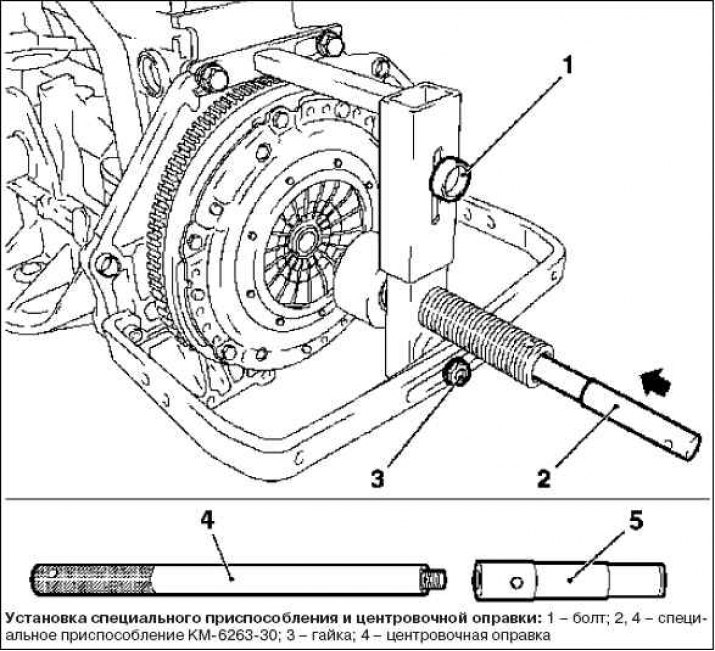
Disconnect the thrust plate and clutch disc.
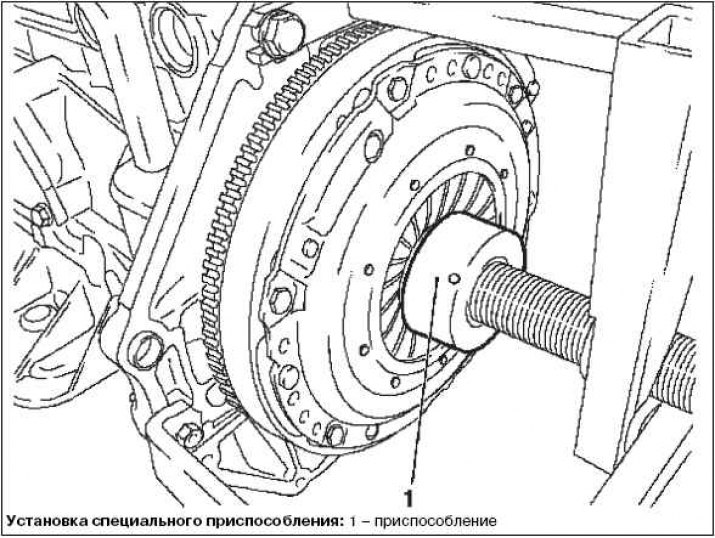
Turn the special tool KM 6263 counterclockwise to the stop and pull out the centering mandrel from the special tool KM-6263-30.
Examination
Check thrust plate and clutch disc for wear.
Replace if necessary.
Note. Clutch discs contaminated with waste products (oil, cleanser, etc.) must be replaced. Check the clutch disc for damage and friction products on the hub and replace if necessary. Do not clean the thrust plate and clutch disc with a high pressure cleaner or washer.
Check the condition of the friction surface of the flywheel for cracks, burn marks and surface wear.
Check the condition of the friction linings of the clutch driven disk and if they have traces of oil or mechanical damage, replace the driven disk.
Check the thickness of the clutch disc linings using a vernier caliper. Linings should protrude above the rivet heads by at least 0.3 mm.
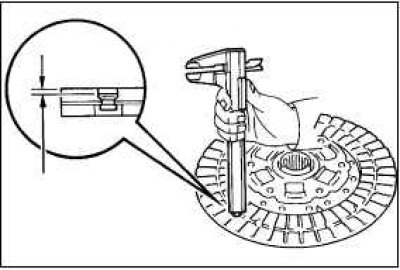
If the thickness of the lining is less than acceptable or the heads of the rivets are close to the working surface, replace them or the clutch disc. Check that the springs are not broken or cracked. Check the splines in the clutch disc hub for wear.
Install the clutch disc onto the gearbox shaft.
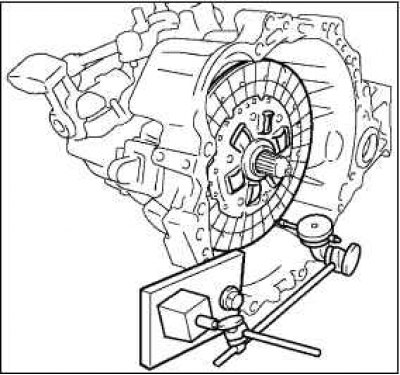
The clutch disc should slide easily and smoothly on the splines of the gearbox input shaft.
Attention! If the clutch disc is being replaced, the clutch release bearing must also be replaced.
Using a dial gauge, check clutch disc runout.
Minimum runout: 0.8 mm.
Using a vernier caliper, check the depth and width of the diaphragm spring petals for wear.
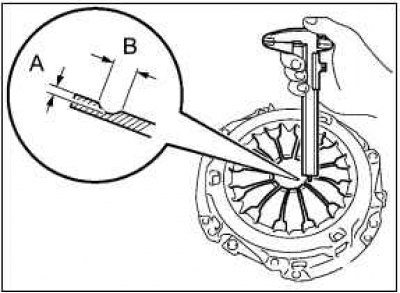
Maximum:
A (Depth): 0.5mm
B (Width): 6.0mm
Note. Slight damage to the friction surface can be removed with fine sandpaper, but if there is any doubt about the condition of the pressure plate, it must be replaced with a new one.
Using a dial gauge, check flywheel runout.

Max runout: 0.1mm
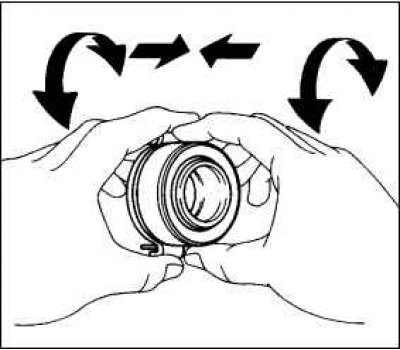
Rotate the clutch release bearing by hand, applying force in the axial direction, check the clutch release bearing.
Note. The bearing is lubricated for life, so no additional lubrication is required.
Note. If necessary, replace the clutch release bearing.
If new parts are installed, be sure to find out which pressure and driven disks are required by the engine designation and its number in order to eliminate an error. If used clutch parts are installed, they must first be checked.
Before installing a new pressure plate, the corrosion-protective grease must be removed only on the working surface. In other places, it is not recommended to remove the grease in any case, because. this can significantly reduce clutch life.
Check the installation of the centering pins on the flywheel.
Clean off any rust on the drive plate spline. Lubricate the gearbox input shaft teeth with a thin coat of MoS2 grease. At service stations, grease G000100 is used for this purpose. After that, move the driven disk on the input shaft so that the hub easily walks on the shaft. Be sure to remove excess grease.
Apply grease to the contact surfaces of the clutch and release fork, fork and pushrod, and the fork support point.
Apply grease to the clutch splines and to the drive shaft splines.
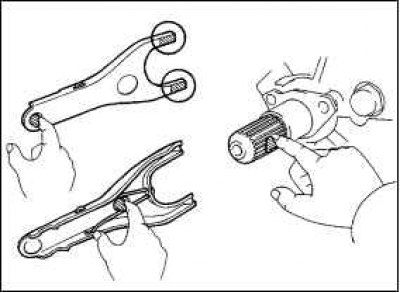
Install the clutch release fork with the clutch release bearing into the gearbox.
Note. After installation, move the fork back and forth to check that the release bearing moves smoothly.
Installation
Note. Letter designation «transmission side» should face the gearbox.
Attach the clutch disc and thrust plate to the flywheel.
Center the thrust plate and clutch disc with a centering mandrel and special tool KM-6263-30.
Note. For clarity, Figure 3.13 shows the clutch without KM 6263.
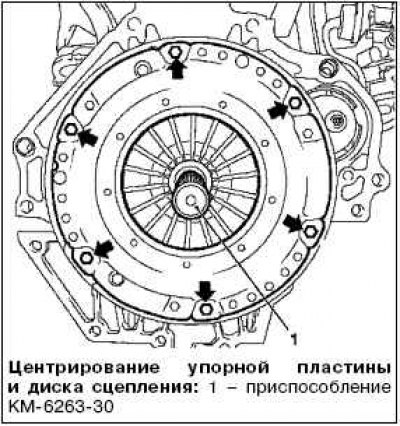
Install 6 new bolts (arrows in the picture).
Note. Do not overtighten the bolts.
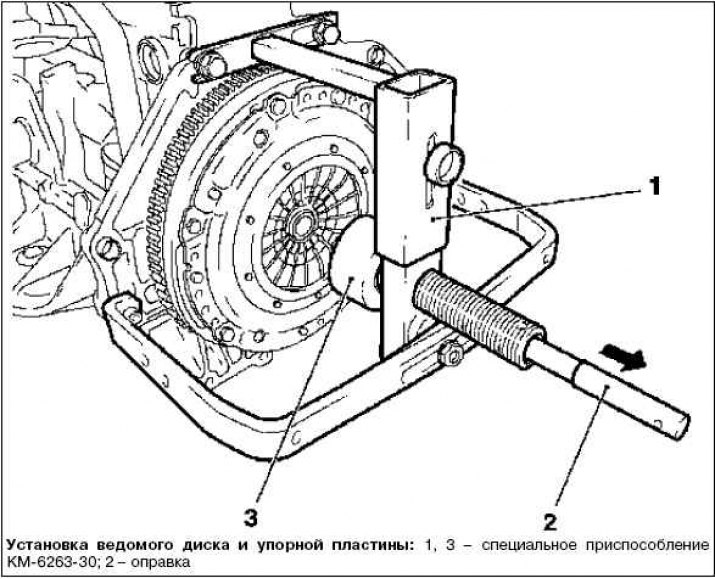
Attach thrust plate to flywheel.
Turn the special tool KM 6263 clockwise to the stop.
Tighten 6 mounting bolts to 15 Nm.
Note. Tighten the bolts crosswise.
Disconnect the KM 6263 special tool from the engine block. Turn counterclockwise to the stop and disconnect the centering mandrel and KM-6263-30.
Turn away 4 bolts of the special adaptation KM 6263 on the block of the engine.
Install the gearbox.
Visitor comments