2. Remove hoses and wires from carburetor, making marks to avoid tangling during reassembly.
3. The jets and float chamber can be accessed by removing the top half of the carburetor, which is attached with five screws. Blow out jets and holes with compressed air, never with wire. If you need to remove the jets, unscrew them carefully with a well-suited tool.
4. Remove the fuel strainer from the inlet pipe.
5. Clean the float chamber. Replace the inlet needle valve if there is wear or if there has already been high mileage. Replace the float if it has holes or other damage.
6. It is not possible to adjust the setting of the top position of the float as it depends on the weight of the float being between 5.75-5.95 grams. However, it is possible to check the initial setting as follows. Turn the carburetor cap over, measure the distance from the connector surface to the farthest edge of the float (Pic. 3.3). The tension spring ball in the needle valve must not be depressed during the test. The distance must comply with the data in the Specifications.
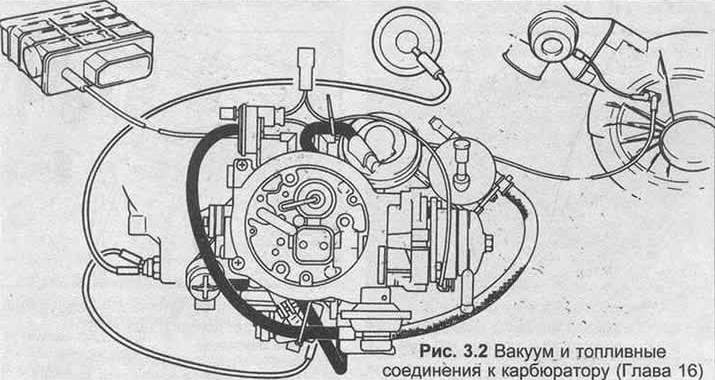
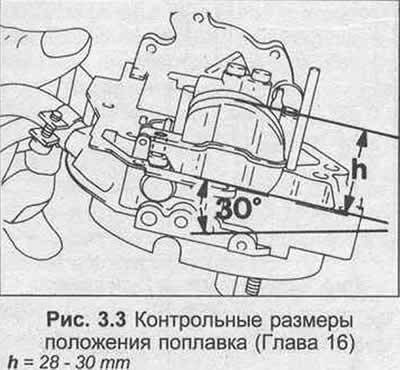
7. Replace the diaphragms in the load enrichment valve and in the accelerator pump. Replace the fuel inlet strainer. Prepare a set of gaskets.
8. To remove the 2nd vacuum chamber, remove the rod from the ball end of the lever and unscrew the suspension screws. When installing the block, the position of the rest of the link should be between 0.5-2.0 mm from the ball end of the lever, as shown in Fig. 3.4. This provides pre-tensioning of the rod when connecting.
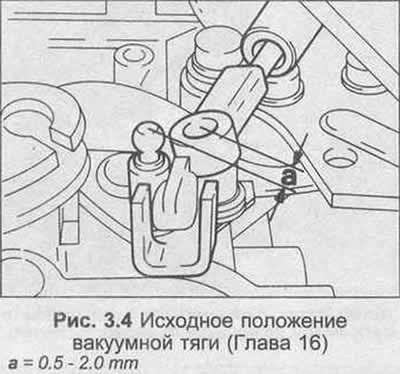
9. The thermostatic valve can be removed by unscrewing the suspension screw (Pic. 3.5).
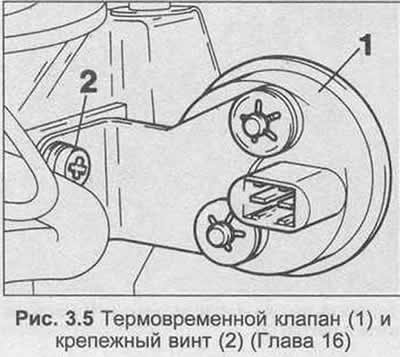
10. Carburetor assembly is carried out in the reverse order of dismantling, use new gaskets and seals. Lubricate the rods with a little oil.
11. See fig. 3.6 and check that the distance between the enrichment pipe and the diffuser is 24-26 mm. Also check that the pipe is vertically above the center of the diffuser.
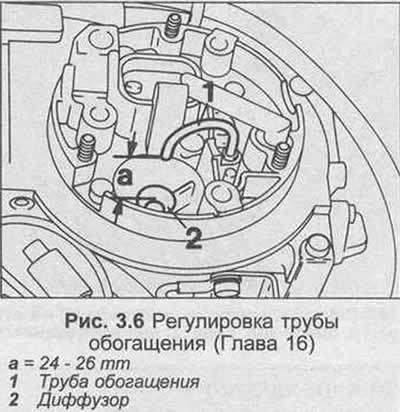
12. The operation of the accelerator pump can be checked as follows (the fuel in the float chamber must be maintained at the correct level). On models with automatic transmission, first adjust the damper (Chapter 17). Rotate the auto choke cam, releasing the fast cooling adjustment screw. move. Place the carburetor over a suitable container, then open and close the throttle ten times for approximately one second, wait about three seconds, and repeat. Divide the amount of fuel collected by ten and compare with the data in the Specifications. If adjustment is necessary, see fig. 3.7, loosen the bolt and reinstall the cam as required, noting that turning the cam clockwise increases the pump output and turning it counterclockwise decreases the pump output.
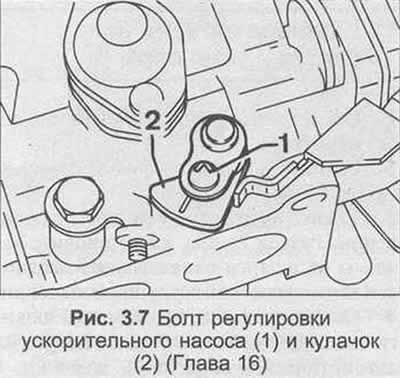
13. Check that the accelerator pump jet is directing fuel towards the notch as shown in Fig. 13. 3.8. If not, you need to remove the carb cap to move the jet.
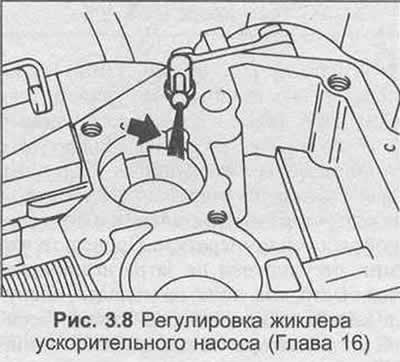
14. See figure 3.9 and check that the 2nd chamber thrust settings are as shown with the 1st chamber throttle at idle. If necessary, bend the plug to correct the installation.
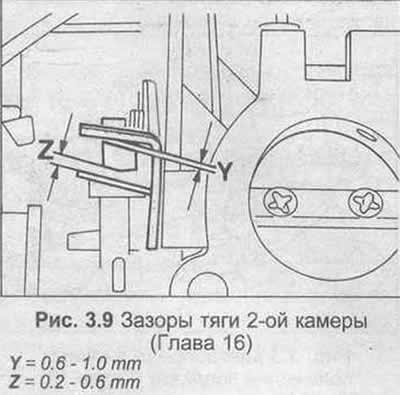
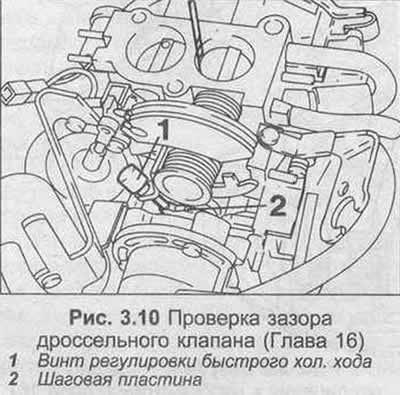
15. Turn the carburetor over, set the fast idle adjustment screw to the highest cam level. Using a twist drill, check the gap between the primary throttle valve and the bushing, compare with the specification for the throttle valve clearance. This provides the initial setting for a higher idle speed. Adjust the fast idle adjustment screw if necessary.
16. To check the choke gap, first check that the descending diaphragm is not leaking, then disconnect the vacuum tube from the diaphragm. Fully close the choke, place the adjusting screw in the highest position of the fast, idle cam. Using a small screwdriver, push the diaphragm rod to the first pressure point. With the pull in this position, using a drill, check «small» air damper gap between air damper and hole (fig 3.11). If necessary, adjust it by turning the adjusting screw of the block. If «small» the air damper gap is correct, push the rod all the way into the diaphragm, then repeat the measurement procedure and check «big» air damper gap. Again, if necessary, adjust the clearance by turning the block adjusting screw.
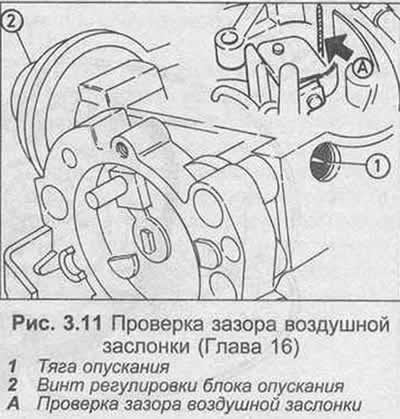
17. If only the air damper gap is correctly adjusted, check the fast, cold cam adjustment. move as follows. Guided by Fig. 3.12, open the throttle, slightly push the throttle lever in the direction of the arrow, then close the throttle again; the adjustment screw should now be set to the second cam pitch. Using a drill, check the gap between the air flap and the hole. If necessary, adjust the quick cool gap. stroke, gently bending the lever (Figure 3.13), be careful not to damage the return springs.
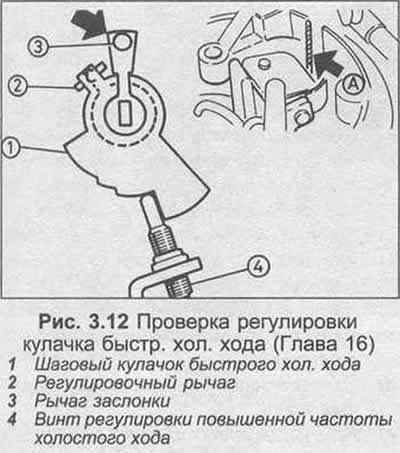
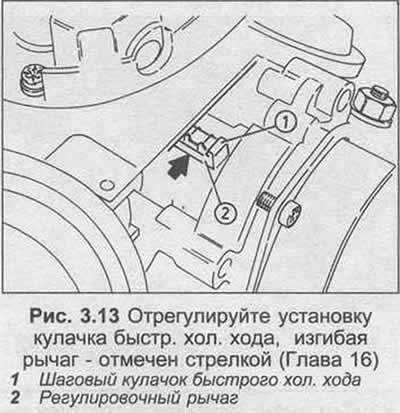
18. Then check the forced opening of the air damper as follows. Guided by Fig. 3.14, rotate the damper lever in the direction of the arrow until it touches the stop. Secure the lever in this position using a rubber band, then fully open the throttle and measure the forced choke opening (size «IN»). If adjustment is necessary, carefully increase the gap using a screwdriver or decrease it using a pair of pliers. After setting the gap, remove the rubber band from the damper lever.
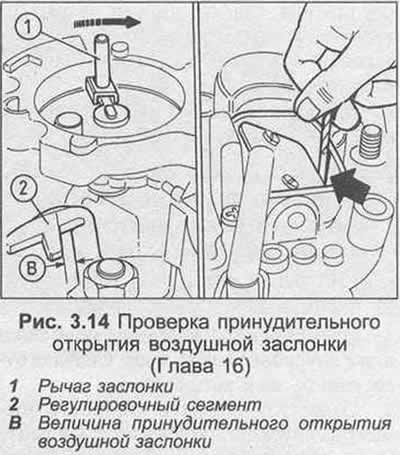
19. Install the throttle cover on the carburetor by inserting the lever into the cover spring loop and aligning the marks (photo).
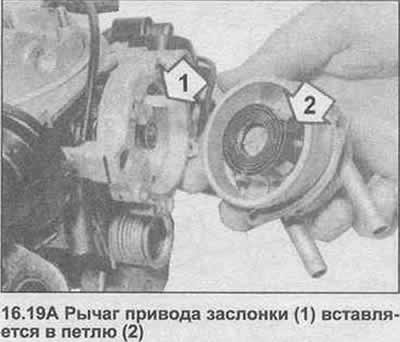
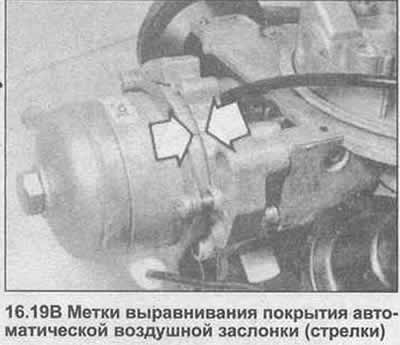
Visitor comments