2. Insert the main bearing shells into the crankcase, the tabs should fit into the special grooves. Note that the center bushing has thrust flanges.
3. Lubricate the liners with clean engine oil (photo).
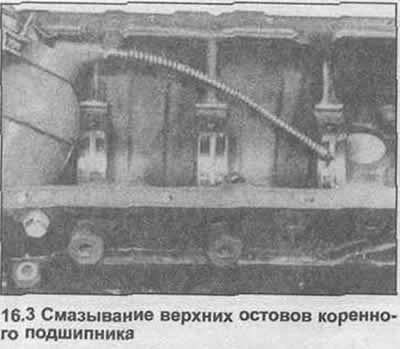
4. Gently lower the crankshaft into the crankcase. Rotate it a few times and check that it is correctly placed by gently hitting the lintels with a mallet (photo).
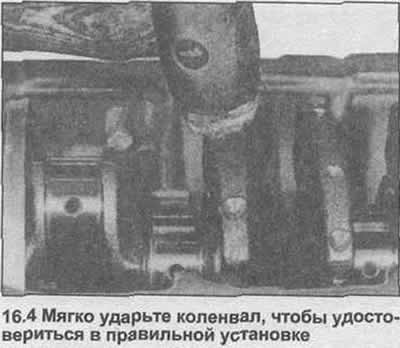
5. Check that the side play of the crankshaft matches the data in Specifications, by inserting a feeler gauge between the ribbed main bearing center shell and the thrust surface of the crankshaft, or by placing a test indicator on the flange at the rear of the crankshaft (photo).
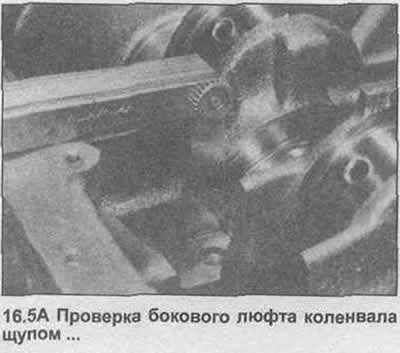
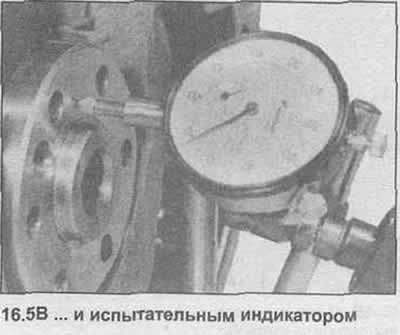
6. Clean the rears of the lower main bearing shells and caps, then reinstall them. Lubricate the bearings with clean engine oil (photo).
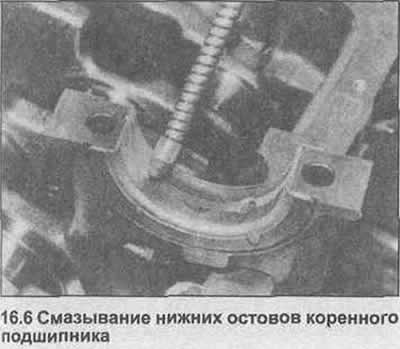
7. Cover the surface of the rear main bearing cap with sealant GM 15 04 200 (8 983 368). Fill the side grooves of the cover with RTV compound or GM sealant 15 04 294 (90 001 851) (photo).
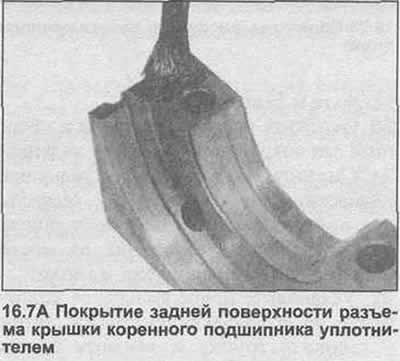
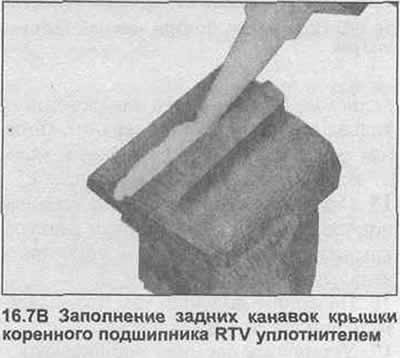
8. Establish a back cover of the main bearing, then insert new bolts of fastening of a cover of the bearing and clamp them the moment of an inhaling regulated specification (photo). If required, a crankshaft rear oil seal can be installed.
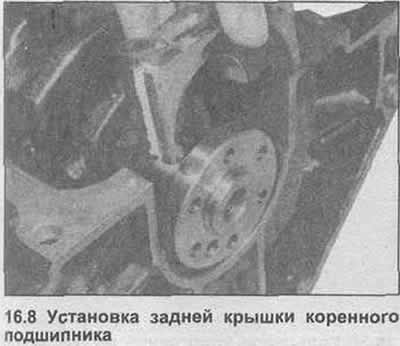
9. Push the seal into the side grooves until they are filled (photo).
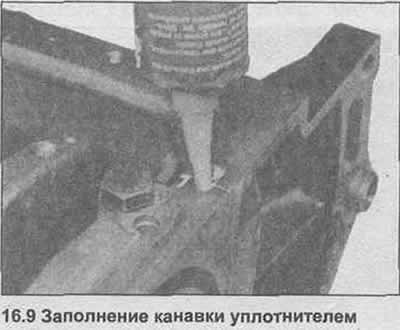
10. Install the remaining main bearing caps, then install new cap bolts and tighten them to the specified torque specification. Make sure that the plane of the front cover is level with the end of the crankcase. Note that the bolts must be tightened with an initial torque, then tightened to a certain angle (photo).
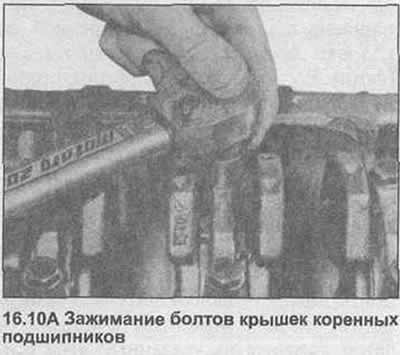
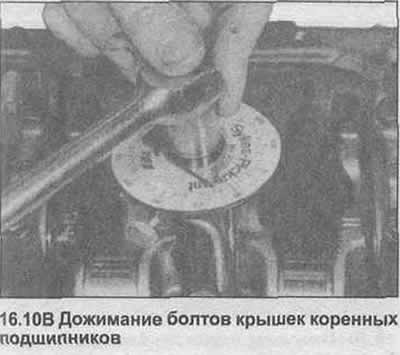
11. Turn the crankshaft and check that it rotates freely with no signs of pinching or stressed places.
12. Lubricate the lugs of the new crankshaft rear oil seal. Cut off a piece of celluloid to use as an oil seal guide, place it on the crankshaft rear flange. Position the oil seal on the bushing and insert it into the rear main bearing cap. You can use part of the pulley to push in the oil seal using two flywheel bolts and the old oil seal (photo). Remove the extractor and celluloid.
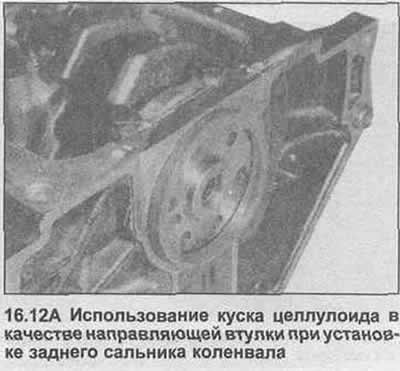
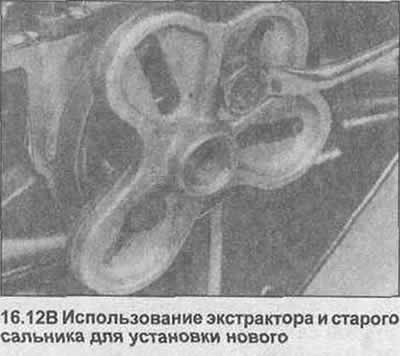
13. Lay the block on its side, lubricate the cylinder bores and crankshaft journals with oil.
14. Place the piston rings around the pistons so that their gaps are 180°apart. In the case of an oil scraper ring, move the gaps in the upper and lower rails 25-50 mm to the right and left of the gap in the center section cut.
15. Clean the backs of the connecting rod bearing shells, caps and connecting rods, then reinstall the bearing shells.
16. Rotate the crankshaft so that the No. 1 cylinder neck is at BDC.
17. Install a piston ring remover on the No. 1 piston, then insert this piston into No. 1 cylinder with the arrow on the piston head towards the front of the engine (photo). The extensions on the back of the piston, the connecting rod, and the lower connecting rod bearing cap must face the rear of the engine.
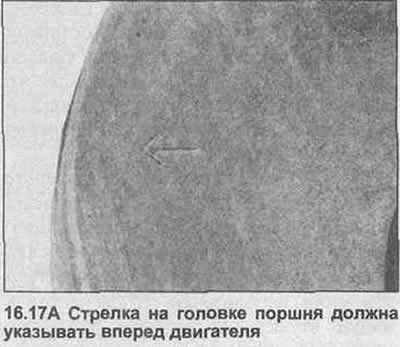
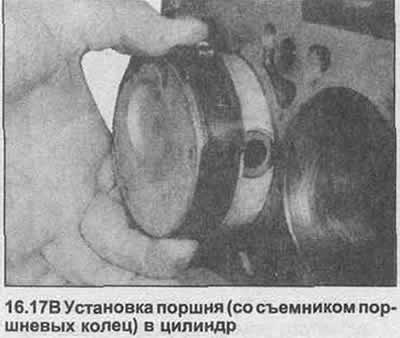
18. Use a hammer handle to drive the piston through the annular compressor, directing the connecting rod to the neck.
19. Establish the bottom cover of the bearing of a rod, then insert new bolts of the bottom head of a rod. Tighten the bolts first to Stage 1 torque and then tighten to the specified angle (see Specifications at the beginning of this section) (photo).
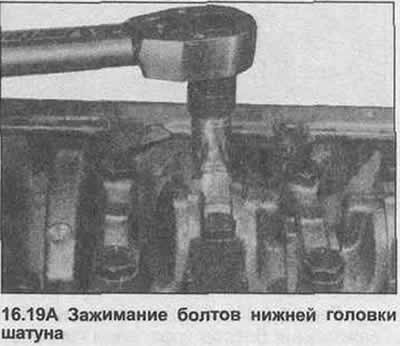
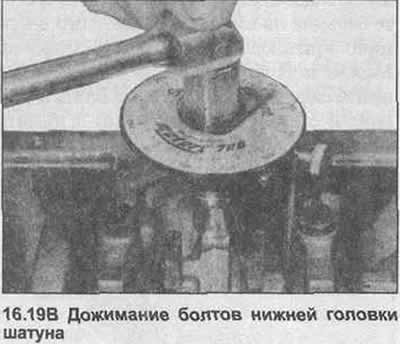
20. Check that the crankshaft rotates freely, taking into account the resistance of the piston rings.
21. Repeat the procedure given in steps 16-20 for the remaining pistons.
22. Turn over the block on the bench.
23. Place a new oil pump gasket on the front of the block, secure it with a little grease (photo).
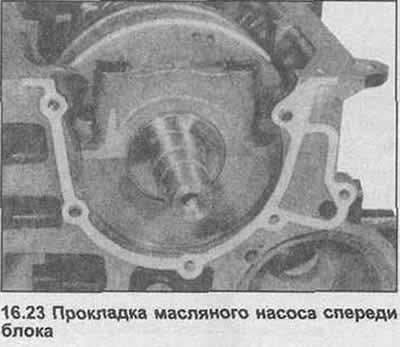
24. If necessary, remove the old oil pump seal.
25. Install the oil pump, then insert and tighten the bolts.
26. Cut a piece of celluloid and wrap it around the crankshaft nose. Lubricate the lugs of the new oil seal, place it on the celluloid. Using a suitable socket and crankshaft pulley bolt, insert the oil seal into place (photo). Remove celluloid and nest.
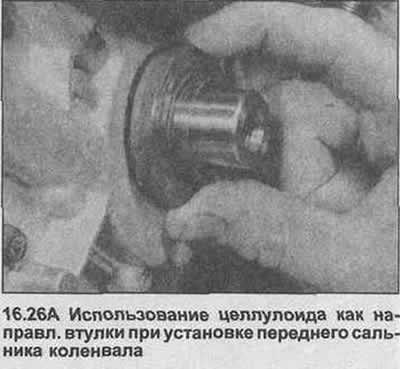
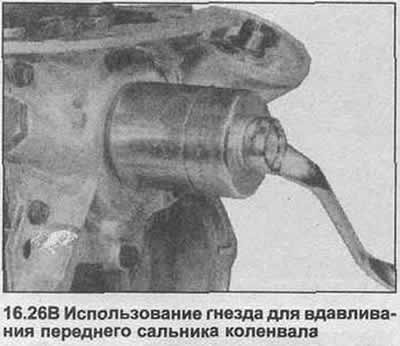
27. Install a new O-ring on the suction tube, then install the tube and tighten the bolts (photo).
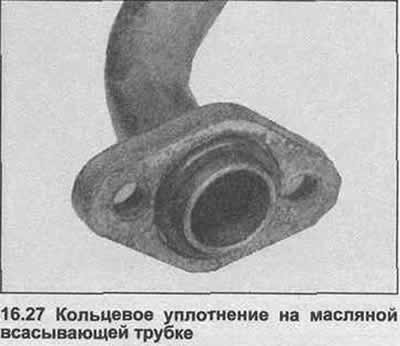
28. Install a new pan gasket on the bulkhead.
29. Apply sealant GM 15 03 294 (90 001 871) on both sides of the gasket in the corners only, place a baffle on the crankcase (photo).
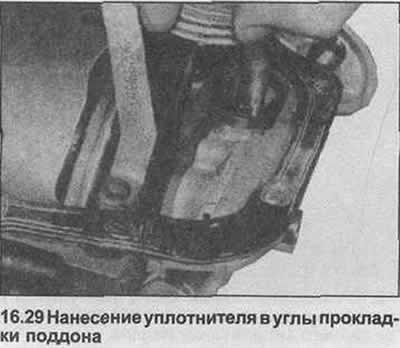
30. Install the pallet. Apply a locking agent to the threads of the bolts, then insert and tighten them evenly in a diagonal sequence to the specified torque specification (photo).
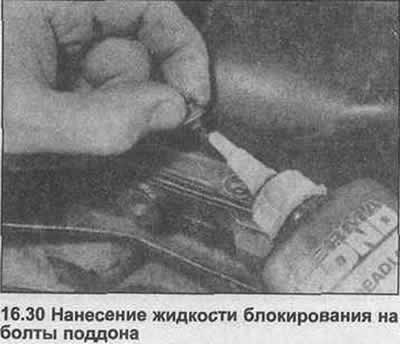
31. Place the engine stand on the workbench.
32. Place the flywheel/drive plate on the rear of the crankshaft. Apply locking agent to the threads of the new bolts, then insert and tighten them evenly, locking the flywheel with the method described in Chapter 9, paragraph 12. Note that the bolts must be tightened to the initial torque and then tightened to a certain angle (photo).
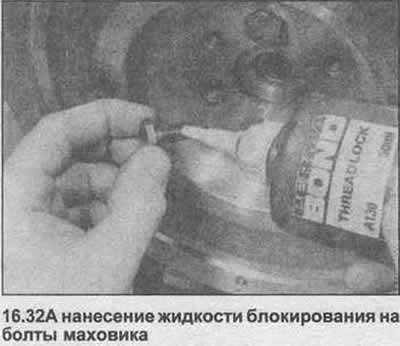
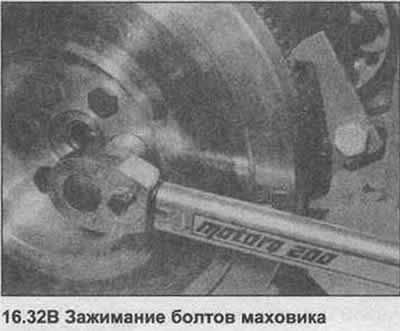
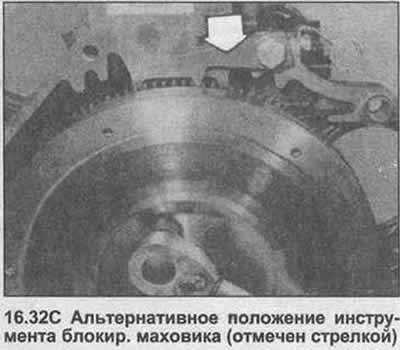
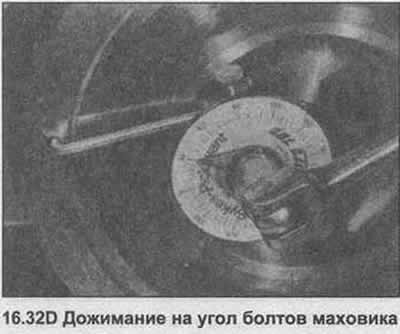
33. Turn the engine so that pistons No. 1 and 4 are at TDC.
34. Check that the location pins are inserted into the block and the connector surface on the block and cylinder head is clean (photo).
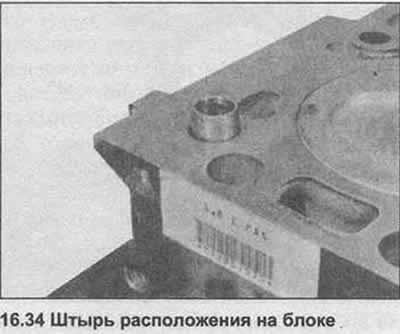
35. Place new head gasket on block with TOP up and forward (photo).
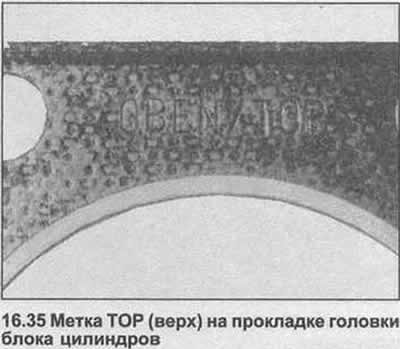
36. Install the hydraulic pushers, thrust pads and rocker arms in the cylinder head in their basic positions (photo). If new hydraulic tappets are used, initially dip each into a container of clean engine oil and squeeze with your hand a few times to fill them up.
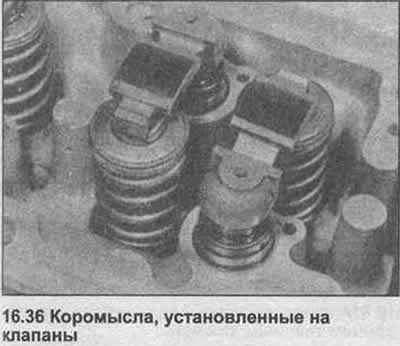
37. Place the cylinder head on the block so that the pins fit into the holes (photo).
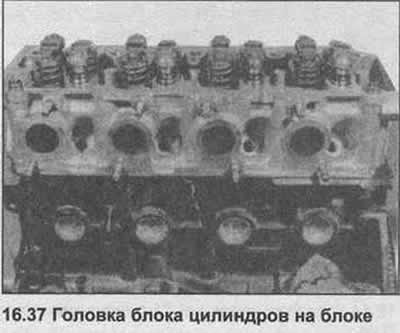
38. Remove the old oil seal in front of the camshaft housing (photo). Clean the bearing surface, hammer in a new oil seal using a block. Lubricate the oil seal lugs with lubricant.
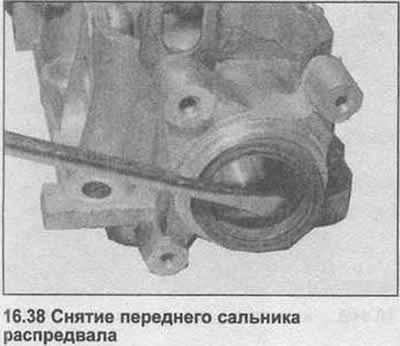
39. Lubricate the running surfaces of the bearing in the camshaft housing (photo).
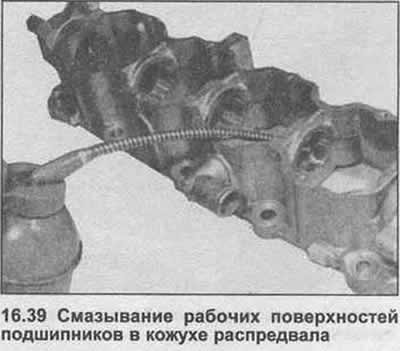
40. Carefully insert the camshaft into the casing. Install the camshaft fixing plate, tighten the bolts. Measure the side play of the camshaft with a feeler gauge (photo), compare it with the data in the Specifications.
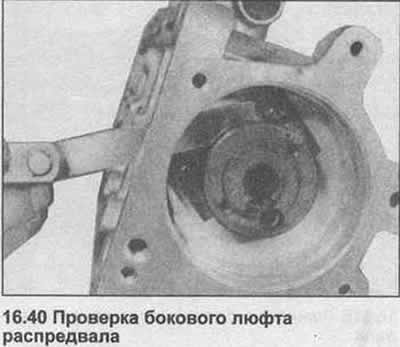
41. Apply the compound to the mating surface of the cylinder head, spread it evenly with a soft brush (photo).
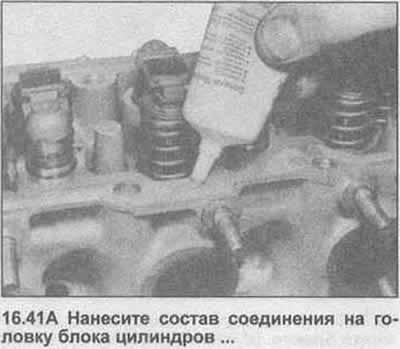
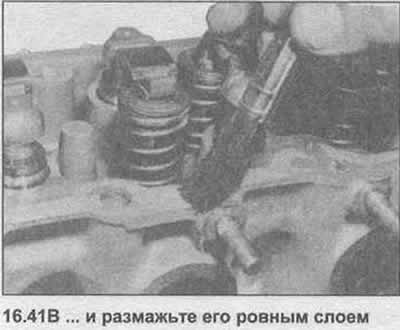
42. Turn the camshaft so that the pin in front is at the top (photo), then lower the camshaft housing onto the head.
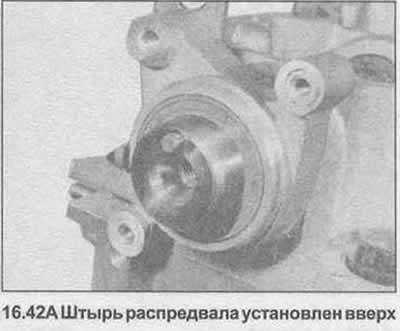
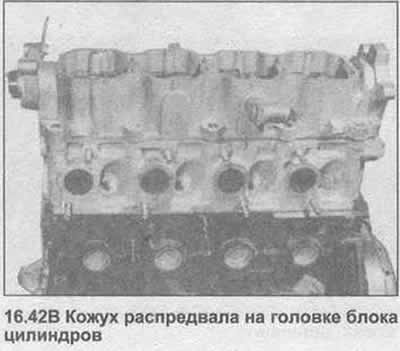
43. Insert new bolts of fastening of a head of the block of cylinders, tighten them in the sequence shown on Fig. 43. 1.3 tightening torque, regulated specification. Note that the bolts must be tightened to the initial torque, then progressively tightened to the specified angle (photo).
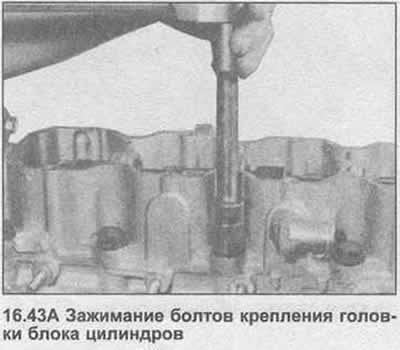
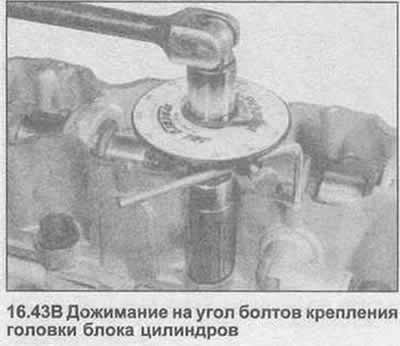
44. Install the crankcase ventilation pipe with a new gasket, tighten the bolts. Install the hose in the camshaft housing, clamp the clips (photo).
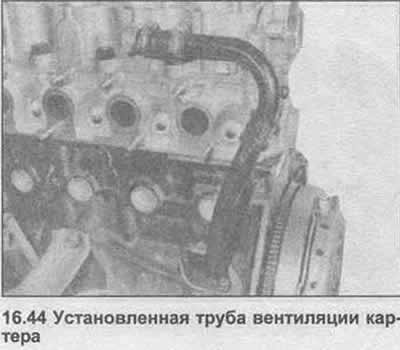
45. Install the front cooling shroud. fluid and thermostat to the cylinder head using a new O-ring. Insert and tighten the bolts.
46. Install the cooling fan hub hanger onto the unit. Insert and tighten the bolts.
47. Lubricate the O-ring of the new oil filter, then screw it by hand into the oil pump housing.
48. Establish a back covering of a gear belt of a drive. Insert and tighten the bolts.
49. Apply silicon lubricant or equivalent to the surface of the water pump in contact with the block. Install a new rubber O-ring.
50. Place the water pump in the block. Insert clamp bolts and washers.
51. Place the sprocket on the front end of the camshaft, insert into the orientation pin. Insert bolt. Fix the camshaft and tighten the bolt with a tightening torque regulated specification. You can use a double end wrench (photo).
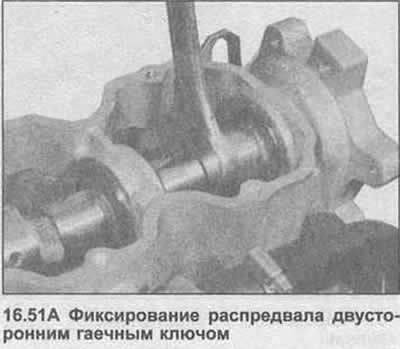
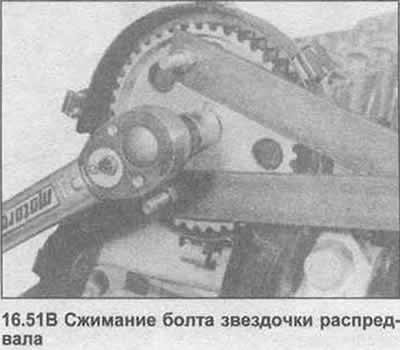
52. Install the gasket, keyway and sprocket onto the crankshaft. Temporarily install the timing belt on the crankshaft, camshaft and water pump sprockets.
53. Place crankshaft pulley/vibration damper on crankshaft sprocket, insert bolts. Insert the center bolt.
54. Fix the flywheel/drive plate using the method described in Chapter 9, paragraph 12. Tighten the outer bolts first, then the central bolt with the tightening torque specified specification (photo). Note that the center bolt must be clamped to the initial torque, then tightened to the specified angle.
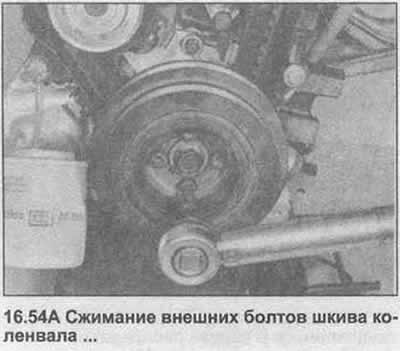
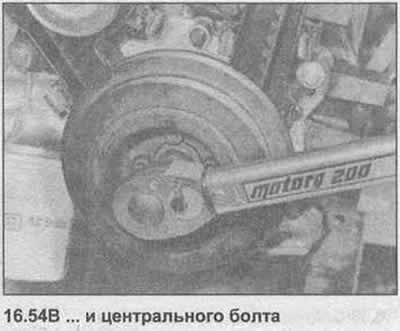
55. Disconnect the timing belt drive, align the alignment marks on the camshaft sprocket and crankshaft pulley with pointers on the rear cover. Reinstall the belt without moving the sprockets and applying some tension by moving the water pump clockwise (photo).
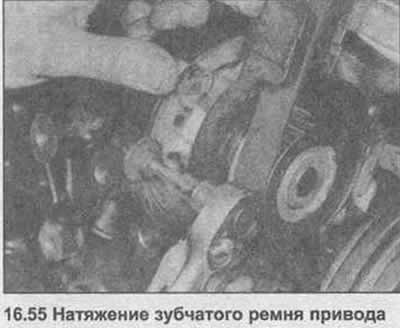
56. Ideally use a GM recommended tensioning tool (K.M-510-A), to adjust the timing belt tension. If not, continue as follows.
57. Turn the water pump clockwise to create a moderate tension on the belt, then tighten the bolts. Turn the crankshaft half a turn clockwise until the belt is tensioned between the crankshaft and camshaft sprockets. Install a tensioning tool between the camshaft and water pump sprockets, take readings and compare them with the data in Specifications.
58. If adjustment is needed, turn water pump clockwise with heating pad to increase tension or counterclockwise to decrease tension. Rotate the crankshaft one full revolution and repeat the test.
59. If there is no tension tool, you can make a rough adjustment by checking if it is possible to turn the belt 90°with your thumb and forefinger (photo).
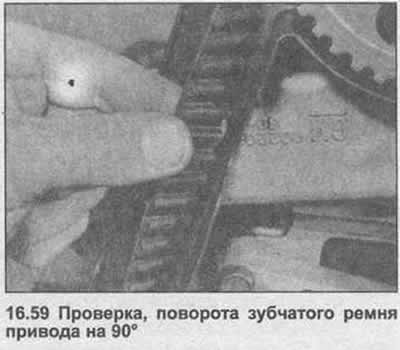
60. Having completed the adjustment, tighten the water pump bolts with the tightening torque regulated specification (Section 2), check the alignment of the alignment marks.
61. Insert and tighten the bolt securing part of the water pump drive cover to the oil pump casing.
62. Install the two timing belt covers.
63. Install the cooling fan pulley. Insert and tighten the screws.
64. Install the camshaft cover with a new plug gasket. Insert and tighten the bolts.
65. On fuel-injected models, install the air valve auxiliary hanger onto the camshaft housing along with a new gasket. Insert and tighten the bolts.
66. Connect the crankcase ventilation hose to the camshaft cover.
67. Insert the engine oil dipstick.
68. Insert and clamp the oil pressure sensor.
69. Using a bar, install a new oil seal at the rear of the camshaft housing. Lubricate the protrusion of the gland.
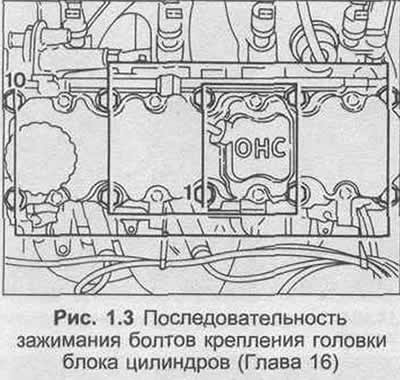
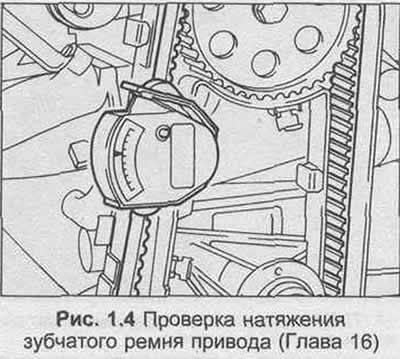
Visitor comments