Fuel from the tank to the injection pump is supplied by a fuel priming pump. The injection pump pumps the incoming fuel under pressure, ensuring its injection into the combustion chambers. The fuel supply occurs in the sequence of the cylinders.
To reduce the content of harmful substances in the exhaust gases, a special diesel catalyst is installed on diesel engines. At the same time, the recirculation system further reduces the amount of nitrogen compounds in the exhaust gases.
A similar effect is achieved by mixing gases and fresh air. As a result, the oxygen content in the exhaust gas decreases. The volume of exhaust gases returned for post-combustion needs to be dosed because their uncontrolled intake leads to the formation of soot and an increase in the content of particulate matter in the exhaust gases. Therefore, the air volume is controlled by a mass flow meter, while the exhaust gas recirculation system is controlled by a microprocessor.
Before entering the injection pump, the fuel passes through the fuel filter, where dirt and condensate are trapped. Therefore, it is extremely important to replace the fuel filter at the time required by the maintenance conditions.
The injection pump does not require maintenance. All moving parts of the pump are lubricated with diesel fuel. The injection pump is driven by a chain from the crankshaft.
The diesel engine control unit recognizes faults and malfunctions in the power system and registers them, creating an error log, where faults are recorded in the form of codes. In the workshop, with the help of a tester connected to the diagnostic socket, the error log is opened and the registered malfunctions can be eliminated in a targeted manner without wasting time and effort searching for them (see illustration 1.0).
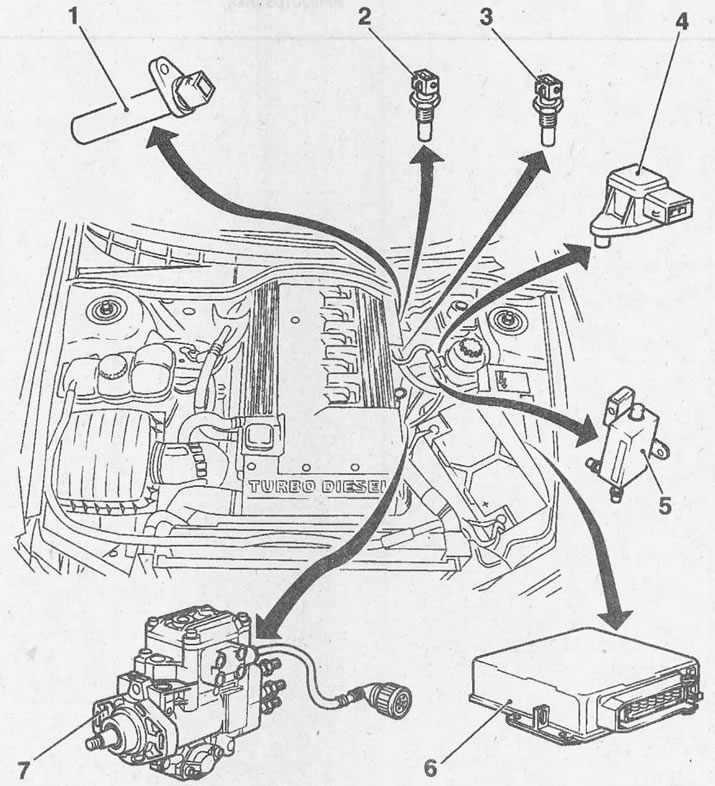
1.0 Components of the power system in the engine compartment. Vehicles with 2.5L engine
1 - crankshaft position sensor
2 - coolant temperature sensor
3 - boost air temperature sensor
4 - boost air pressure sensor
5 - exhaust gas recirculation valve
6 - engine control unit
7 - injection pump
Diesel engines use two distinct fuel injection methods: swirl or pre-chamber injection and direct injection.
Vehicles with a 2.5 liter swirl chamber injection system
Fuel is supplied to the preliminary chambers of the cylinders, where the hot mixture immediately ignites. Upon subsequent compression, the gases swirl, mixing well with the injected fuel, and the mixture burns quietly. The remaining, unburned part of the mixture is blown by the overpressure arising during combustion directly into the combustion chamber. There, the fuel burns completely.
Vehicles with 2.2L direct injection engine
This engine uses a VP44 high-pressure fuel pump with a radial piston arrangement and creates an injection pressure of up to 1800 bar. A turbocharger with variable turbine blade geometry is used for air injection, providing high engine acceleration throughout the entire speed range.
Vehicles with a 2.5L engine with rail direct injection
The fuel injection pressure for these engines is about 1350 bar. During injection, the fuel is very finely atomized and burns with the release of a large amount of energy.
The fuel supply to the injection pump is carried out by a fuel supply pump, which allows the injection pump to create a sufficiently high pressure even at low engine speeds for fuel injection.
From the high-pressure fuel pump, fuel enters the so-called distribution rail, and from it - to the nozzles of the corresponding cylinders. The distribution rail serves as a fuel tank in which a constant pressure is maintained.
The required volume of injected fuel is determined and set by the microprocessor, which regulates the duration of the opening of the valve injectors
Due to the improved cold start properties, engine preheating is only necessary at temperatures below -10°C.
Turbocharger
OPEL diesel engines are equipped with a turbocharger. In the turbocharger, two turbine wheels are installed on one shaft, which are located in housings separated from each other.
The turbine wheels are driven by exhaust gases. They bring the speed of the supercharger shaft to 120,000 rpm. And since the rotors of the exhaust gas and the supply air sit on the same shaft, air is forced into the cylinders with the same frequency.
Due to the good filling ratio in existing engines, power gains of up to 100 percent can be achieved.
Along with an increase in engine power, the use of a turbocharger also increases torque, which is especially important from the point of view of achieving good engine elasticity. In contrast to the internal combustion engine, the diesel engine does not need to reduce compression due to air boost, which ensures that the energy of the fuel is fully utilized even at low engine speeds.
The turbocharger is an extremely precisely manufactured unit. Therefore, in case of repair, it is recommended to contact only a specialist. As a rule, in the event of a malfunction, the turbocharger is replaced completely.
Visitor comments