Attention! If automatic ventilation does not occur and the pump is not manually controlled, then:
- Fill the fuel filter with fuel.
- When working on the injection system, the following cleanliness rules must be strictly followed:
- Fill the injection pump (injection pump) fuel.
- Slip the car.
These activities will help remove air from their food system.
Attention! If the engine does not start, check the fuel supply to the injectors. Unscrew the nuts from the two injectors and start the engine without preheating until the fuel appears on the nuts. Tighten the nuts and start the engine.
Driving in winter
The fluidity of diesel fuel decreases with decreasing temperature due to the paraffin content in it. Therefore, oil refineries add special additives to diesel fuel that allow the engine to start even at -15°C. It is also recommended to install a fuel filter heater. They are produced by BOSCH OPEL ET 813170 (90271789).
If a filter heater is not installed, you can add gasoline to summer diesel fuel.
Add gasoline in advance so that the filter and fuel lines are cleared of dense diesel fuel.
Since this additive reduces engine power, add only a certain amount, see table.
Attention! Do not mix diesel fuel with super gasoline.
Fill the car tank with gasoline first, then diesel fuel.
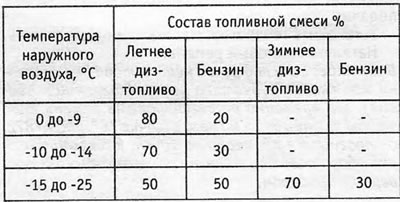
If at very low temperatures the engine does not start due to thickening of the fuel, it is recommended:
- Remove the fuel filter and heat it in a water bath until the diesel fuel liquefies.
- Replace the fuel filter.
- Have a heated garage.
- Spray the injection device with hot water.
Attention! Do not heat the injection device with a blowtorch!
Injection system repair
1 — Before disassembling, thoroughly wipe the parts with gasoline.
2 - Place the removed parts on clean foil or paper and cover. Do not use fluffy rags.
3 - Cover the holes if the repair is delayed.
4 - Install only clean parts.
Remove new parts from packaging only before installation.
Do not install parts that have been stored for a long time without packaging.
5 - During repairs:
- Do not use compressed air.
- Do not move the car.
- Make sure that diesel fuel does not get on the cooling system hoses.
Replacing and draining sediment from the fuel filter
The water from the filter is drained every 5,000 km, the filter is replaced every 30,000 km.
Draining
Place a container to drain the sediment.
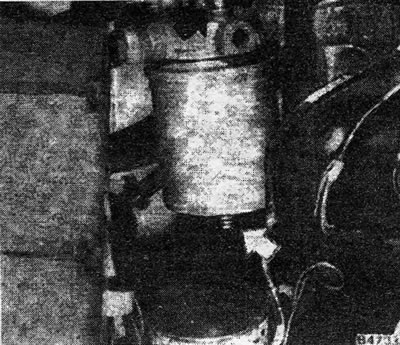
Unscrew the air bleed screw one turn (arrow from above) and sediment drain screw (bottom arrow).
Release about 100 cm of liquid.
Attention! A large amount of liquid indicates porosity of the ventilation hoses. Check and replace all black, porous fuel tank hoses with fabric-covered hoses.
Screw in the ventilation and drain holes.
Replacement
To unscrew the filter, use an oil filter wrench or a leather belt.
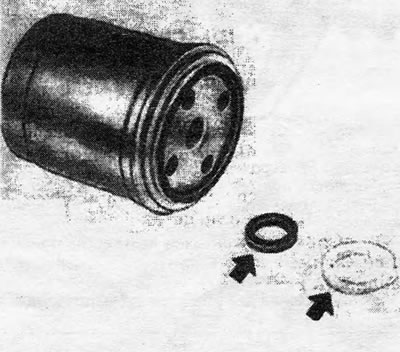
Attention! The filter comes complete with an O-ring and a synthetic material holder (arrows).
The sealing ring is installed on the filter and secured with a holder.
Attention! If the filter is installed without an o-ring, this may lead to engine damage.
Lightly lubricate the outer sealing ring of the new filter with diesel fuel.
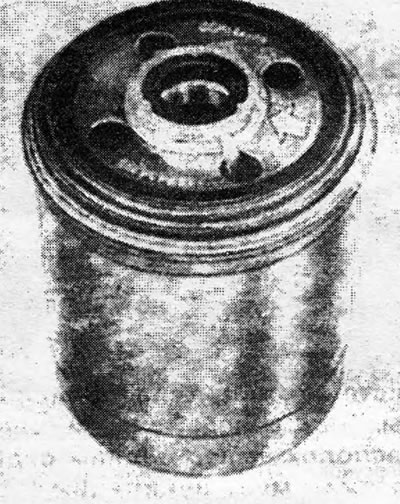
Screw the filter in by hand.
Start the engine. At idle speed, after repeatedly applying gas, fuel should flow through the transparent hose without bubbles.
Check for leakage.
Removing and installing the solenoid valve
The solenoid valve interrupts the fuel supply after the engine is stopped.
Removal
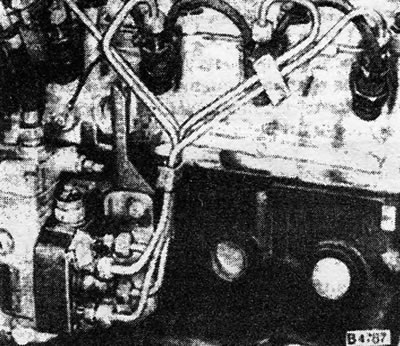
Disconnect the cable from the valve.
Unscrew the valve.
Installation
Screw in the solenoid valve with a new sealing ring and tighten to 2.5 Nm.
Attention! If tightened too tightly, there is a risk of a short circuit in the housing.
Connect the electrical wiring.
Checking and adjusting idle speed
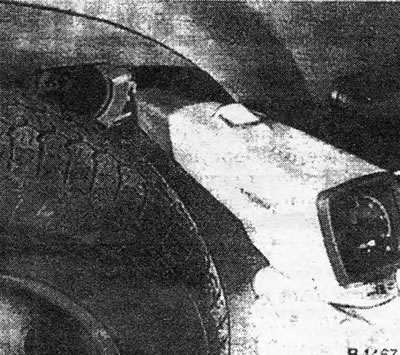
To adjust the idle speed, a diesel tachometer operating on the photo principle is used.
Draw a line on the shoulder of the V-belt pulley 1-2 cm wide.
Warm up the engine to an oil temperature of 50-70°C.
The cold start accelerator button must be recessed.
All electrical consumers are turned off.
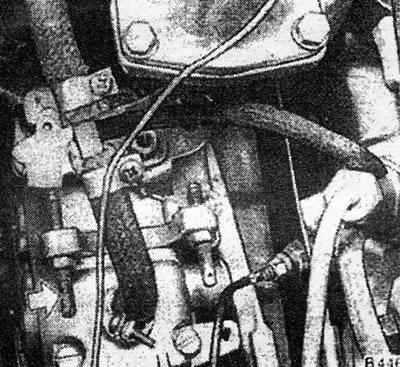
Measure the idle speed with a tachometer.
Loosen the locknut of the adjusting screw.
Adjust idle speed: 16D engine - 850±50 rpm, 16DA engine - 850±30 rpm. (arrow).
Attention! Set the idle speed accurately.
Lock the adjusting screw and coat with varnish.
Checking and adjusting limit speeds
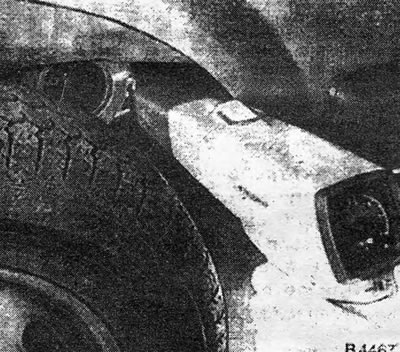
To adjust the maximum speed, a diesel tachometer is used, which operates on the photo principle.
Draw chalk lines on the shoulder of the V-belt pulley 1-2 cm wide.
Warm up the engine to an oil temperature of 50-70°C.
The cold start accelerator button must be recessed.
All electrical consumers are turned off.
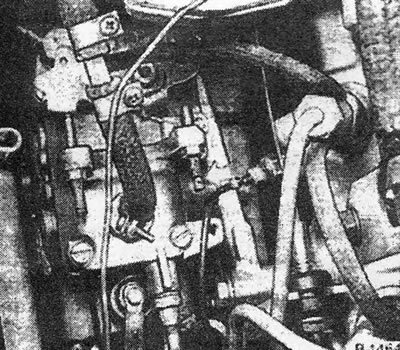
Give full throttle and measure the speed with a tachometer.
Use the adjusting screw to set the speed to 4800 rpm.
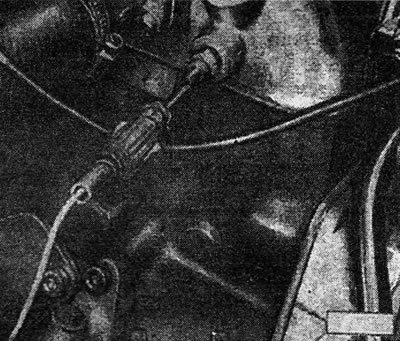
Checking the glow plugs
Remove the connecting cable and the glow plug current bar.
Connect a test lamp to the positive terminal of the battery, connect the second end of the wire in series to the glow plugs.
The spark plugs are working properly if the lamp lights up.
The spark plug is faulty if the lamp does not light up. Replace. If the glow rods are burnt, pay attention to the instructions.
Candles with burnt rods
Burnt filament rod (pic.) - a consequence of a faulty jet, not a glow plug. A similar malfunction is a lack of the internal, rather than the external part of the spark plug. If such candles are found (arrow, fig.) It is not enough to simply replace them; you need to check the injectors for spray, noise, pressure, and tightness (factory work). In this case, pay special attention to ensure that the spray pattern during sharp, energetic movements (4-6 pumping/sec) was flawless.
Removing and installing injectors
A faulty injector causes severe knocking in the engine. Carry out the check at idle speed, turning off the injectors one by one. If the knocking noise disappears after disconnecting the injector, it means it is faulty. Replace. You can also check at high idle speeds, turning off the injectors one by one. If, after turning off the injector, the engine speed remains constant, then this injector is faulty. Checked with a pressure gauge (factory work). For faulty injectors:
- Knocks in one or more cylinders.
- The engine gets very hot.
- Power drops.
- Thick exhaust gases.
- Increased fuel consumption.
Removal
Clean the injection lines with fuel. Disconnect them from the pump and injectors.
Remove the fuel return lines. Unscrew the injector holder.
Remove the wave washer, thermal insulator and copper O-ring.
Clamp the injector holder in a vice using soft spacers. Remove the nozzle.
Check the condition and position of the nozzle needle, wear and damage to the nozzle. Remove carbon deposits with a wooden spatula.
Attention! Do not use for cleaning sharp, scratchy objects. Don't confuse the injectors.
The needle should be inserted freely into the nozzle under the influence of its own weight.
Installation
Assemble the nozzles and holders.
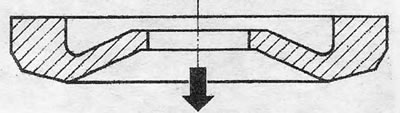
Place new O-rings into the injector holes in the cylinder head. Install insulators with a smaller diameter towards the block head. Place o-rings on the insulators. Install the washers on the insulators as shown in Fig. (arrow).Install the injectors together with their holders and tighten to 70 Nm.
Install the fuel lines and tighten the nuts to 25 Nm.
Visitor comments