Hydraulic module
It is located on the left in the engine compartment: the module is installed between the brake pipes from the master brake cylinder and the brake pipes to the wheel brakes. In accordance with the signals from the electronic control unit, the pressure on the wheel brakes either remains constant, or decreases, or increases again. But the pressure in the brake master cylinder cannot get higher than what you create by pressing the brake pedal. Pressure control is handled by eight quick-switching solenoid valves, i.e. two for each wheel. If the solenoid valves are de-energized, the pressure rises. If the maximum current is applied, the pressure drops, and at a moderate current, the pressure is maintained. Of particular interest is the pressure reduction phase: brake fluid that is squeezed out of the brake master cylinder can't just leak out somewhere (as a result, the brake pedal would be fully depressed), then the brake fluid is pumped by a powerful return pump back to the brake master cylinder. You notice this in the brake pedal, which begins to pulsate slightly when the return pump is working - ABS begins to function.
If you listen carefully, you can also hear the noise from the pump. Due to the silencer in the hydraulic module, the noise is slightly suppressed.
Speed sensor
A total of four sensors record the speed of rotation of each individual wheel and transmit this information to the electronic control unit. Based on it, the control device can, in turn, regulate the operation of the hydraulic module.
The speed sensors themselves consist of a magnetic core and a coil and are mounted at a short distance from the toothed disk - the rotor. The rotor - its name speaks for itself - rotates with the wheel and causes the teeth to rotate along its perimeter past the sensor faster or slower depending on the speed. Each tooth passing under the sensor induces a short voltage rise in the sensor. In this way, an alternating voltage is created in the sensor, which changes its frequency in accordance with the speed of rotation of the wheel. The resulting signal is processed by the electronic control unit as information about the number of wheel revolutions.
In the Vectra, the rotors are forward on the steering knuckle. At the rear, the speed sensors are integrated into the wheel bearing modules.
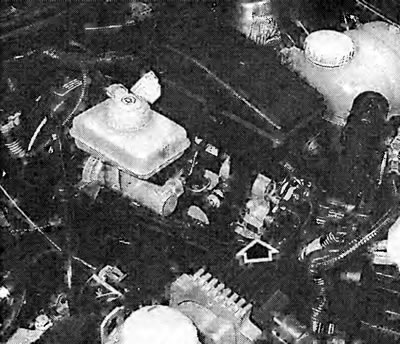
The hydraulic module of the anti-blocking system is located in the engine compartment on the left.
Electronic control unit
The anti-lock wheel control unit is mounted directly on the hydraulic module. It processes the information coming from the speed sensors. At the same time, it controls the hydraulic module so that the wheels do not block. In addition to the complex signal processing and the subsequent logic part, the control unit also has a blocking circuit. With its help, the device can check itself, recognize external defects and control the operating voltage. If an error is detected, the ABS is turned off and the control light on the dashboard lights up. Further, the control unit has a program memory and is capable of self-diagnosis. The error is stored in memory for later troubleshooting. To do this, the workshop has a reading device that is connected to the connector under the center console, as a result of which the excitation and ground diagnostic wire is short-circuited. In this way, faults are shown on the display of the reader and faults can then be corrected.
Electronic brake force distribution
The Vectra dispenses with the traditional brake force regulator on the rear wheels. Instead of mechanical or hydraulic pressure control, an ABS hydraulic module is used for electronic brake force distribution.
The control unit monitors the deceleration of the wheels through a speed sensor on each rear wheel and compares the performance of the front and rear axles. If the braking forces on the rear axle are too high, the pressure is quickly reduced by means of the solenoid valves in the hydraulic module (adapts to optimal wheel deceleration). Thus, excessive braking of the rear axle wheels is not allowed.
Visitor comments