Fuel pressure check
The fuel pressure can only be accurately measured with measuring equipment in the workshop.
- If incorrect fuel pressure is suspected, disassemble the pressure regulator.
- To do this, unscrew the four bolts with torx holes.
- Check if the diaphragm is damaged or if dirt has accumulated.
- When installing, make sure that the diaphragm is correctly positioned in the groove of the throttle body.
- Tighten the bolts to 2.5 Nm.
Injection valve check
- Checking with the engine running: its oil temperature must be at least 60°C, this corresponds to a ten-minute drive after starting a cold engine.
- Remove the air intake pipe on the injection module.
- Start the engine and let it idle.
- Observe the jet of the injection valve. The jet injected by it should be even and directed at the throttle valve.
- Stop the engine to check the valve for leaks.
- With the engine off, no more than 2 drops per minute should come out.
- The checks described below are only carried out if the engine does not start.
- Remove the air intake pipe on the injection module.
- Have an assistant turn the engine over with the starter.
- The injection valve should inject fuel.
- If not, disconnect the connector on the injection valve.
- Connect an ohmmeter to both terminals (to injection module).
- At an air temperature of about 20°C, the device should show 1.4-1.6 W.
- With a hot engine, the resistance value rises to about 1.6-2.1 W.
- If these values are not obtained, the injection valve is faulty.
- When dismantling, unscrew the torx bolt and remove the bracket.
- Use a screwdriver to pry the injection valve out of the housing.
- Use new O-rings when installing. Lubricate the fixing bolt with safety compound and tighten to 3 Nm.
- Checking the voltage supply to the injection valve is carried out if the valve, despite the correct values, does not inject fuel.
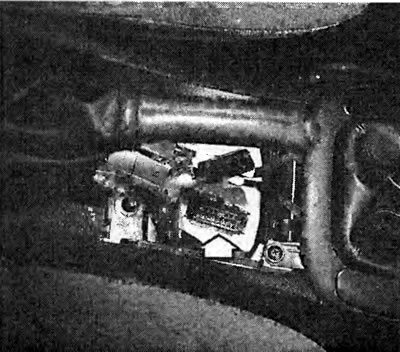
Our Vectra diagnostic connector (arrow) located in the middle console. The diagnostic connector is visible after removing the cover under the handbrake handle.
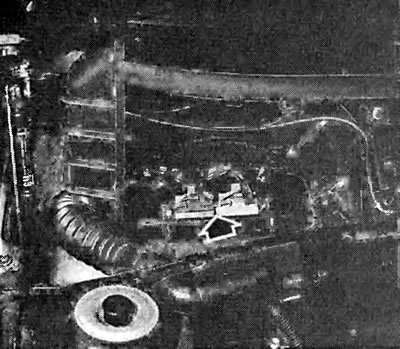
The photo shows the exposed ignition/injection control unit on the right in the engine compartment under the water repellent.
- Connect an LED indicator—do not use anything else—to both middle pins in the disconnected connector.
- Operate the starter: the LEDs should light up, otherwise the conductivity in the wires is broken or the control unit is faulty.
Throttle Potentiometer Check
Throttle potentiometers are manufactured by two different suppliers. They have the same appearance and function, but when checking the potentiometer, they give different resistance readings. The manufacturer's CTS potentiometer has the inscription CTS in the rounding at the top left, the NEI potentiometer does not have such an inscription.
- Ignition off.
- Disconnect the connector on the potentiometer.
- Connect an ohmmeter to the terminals «A» And «IN» on the potentiometer.
- Read the reading on the ohmmeter with the throttle closed. Potentiometer NEI -4.0-6.0 kW; potentiometer CTS - 4.0-9.0 kW.
- Connect an ohmmeter between the terminals «IN» And «WITH». Measurement result with NEI potentiometer: 3.0-4.0 kW and with CTS potentiometer: 1.0-3.0 kW.
- Now slowly open the throttle and read the ohmmeter at full throttle - potentiometer NEI 6.0-7.0 kW; potentiometer CTS 5.0-10.0 kW.
- If the named values are not obtained, then the throttle valve potentiometer is defective
- The potentiometer is attached with two torx bolts to the throttle body injection module.
- When installing a new potentiometer, tighten the screws to 2 Nm.
Checking the stepper motor that controls the supply of the working mixture at idle
- Disconnect the connector on the stepper motor.
- Install a 6V battery charger and connect it alternately to the terminals «A» And «IN», then «WITH» And «D». You can hear the pusher going in and out.
- If so, then the stepper motor that controls the flow of the working mixture at idle is in order. If not, replace it.
- Anyone who does not believe the results obtained can check the resistance of the winding between the terminals «A» And «IN», «WITH» And «D». It should be equal to 50-65 W.
- If a new stepper motor is installed, then it must be ensured that the distance between the end of the pusher and the housing flange does not exceed 28 mm. If necessary, gently press the pusher in.
- Insert screws with safety mass and tighten to 3 Nm.
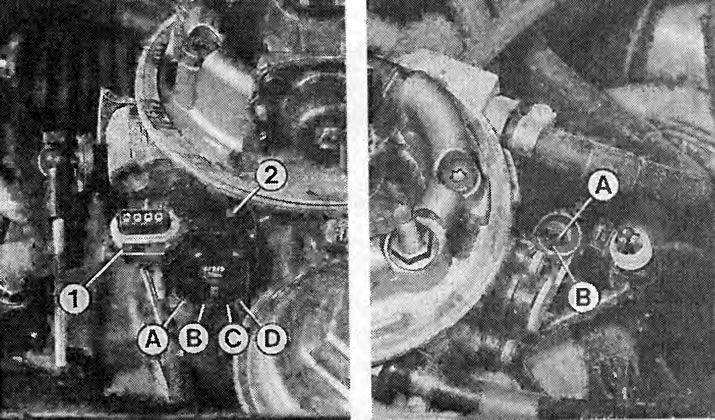
Left: Stepper motor test (2), which controls the supply of a combustible mixture at idle: disconnect the connector (1), switch the battery charger to 6V and connect to the terminals in turn «A» And «IN» or «WITH» And «D».
On right: To test the throttle potentiometer, to its terminals «A» And «IN» ohmmeter is connected.
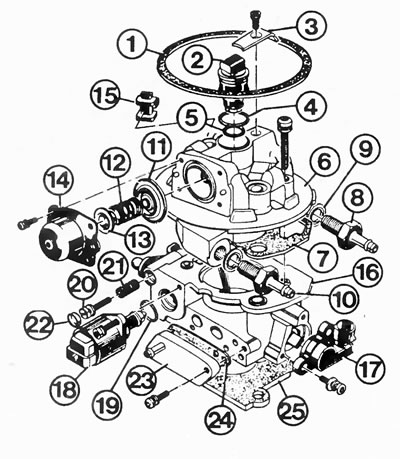
Units of the Multec central injection system:
1 - air filter gasket;
2 - injection valve;
3 - injection valve bracket;
4, 5 - injection valve O-ring at the top or bottom;
6, 1 - upper part of the throttle valve injection housing with gasket;
8, 9 - fuel supply pipe with gasket;
10 - fuel return pipe;
11-14 - diaphragm, spring, spring seat and fuel pressure regulator cover;
15 - rubber tip of the connecting wire;
16 - throttle valve detail;
17 - throttle potentiometer;
18 - idle stepper motor;
19 - O-ring;
20-22 - idle set screw with spring and cover (seal);
23, 24 - flange of vacuum connections with gasket;
25 - gasket for the housing of the injection module / intake manifold.
Checking the pressure gauge in the intake manifold
The workshop uses a vacuum pump to accurately check the intake manifold pressure gauge. An amateur can carry out a temporary check also without a vacuum pump.
- Connect a voltmeter to the intake manifold pressure sensor. To do this, insert the needle into the green wire (terminal B). Make sure the needle does not hit bare metal (weight).
- Connect the positive terminal of the voltmeter to the needle. Attach the negative terminal to ground.
- Turn on the ignition. The voltmeter should show 4.2-5.3 V.
- Start the engine and leave it to idle. Now the voltmeter shows 0.52-1.7 V.
- Raise the engine speed. The voltage rises and falls alternately.
- If the readings are correct, then the intake manifold pressure gauge is OK.
Checking the traction shutdown
- Remove the upper part of the air filter.
- Start the engine, rev up to 3000 rpm and close the throttle sharply.
- The clearly visible jet from the injection valve will be momentarily interrupted at this point. In this case, the traction shutdown is in order.
- If not, check throttle potentiometer, intake manifold pressure sensor and control unit (In workshop).
Checking the coolant temperature sensor
With a built-in thermometer, you can check if the temperature sensor is working properly. The sensor is located under the injection system in the intake manifold.

- Disconnect the wire connector on the temperature sensor and unscrew the sensor from the intake manifold. Collect the escaping coolant in a container.
- Hang the sensor in a pot of water, heat the water and connect an ohmmeter to the connector pins.
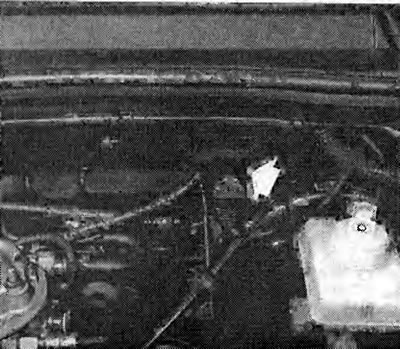
The photo shows the pressure sensor in the intake manifold on the right, next to the brake booster. Read about its purpose on page 77.
Check the respective resistance values at the above temperatures.
If the values match, then the temperature sensor is OK.
Checking lambda control
For this purpose, a voltmeter with a suitable lower measuring range, which amateur electronic engineers own, is used.
- Checking the voltage supply to the lambda probe: disconnect the wire connector of the lambda probe. The connector is located in the mount on the gearbox.
- Connect a voltmeter between the signal wire (brown/blue wire) and mass.
- Turn on the ignition. The meter should show 430-470 mV. If the device does not show anything, check the wire along the entire length to the control unit.
- Checking the lambda probe: connect the wire connector.
- Warm up the engine.
- Insert the needle into the signal wire of the probe. Connect a voltmeter between the needle and ground. Pay attention that the needle does not touch the mass (short circuit danger).
- Let the engine run at about 1500 rpm.
- The meter should show short, rhythmic voltage fluctuations between 50 and 950 mV.
- No voltage fluctuations: defective lambda probe (replace), the combustible mixture is constantly lean or rich (check injection in the workshop) or faulty control unit (check in workshop).
Tip: The main condition for a functioning lambda control is the correct basic idle speed setting, i.e. the CO content must be correct, otherwise the control will always be at the end of the control range. The same applies if the air-fuel mixture is severely lean due to the side air.
Replacing the lambda probe
The probe thread is lubricated with a special anti-seize lubricant. It consists of liquid graphite, which burns during operation, and glass beads. The new probe is supplied with this lubricant, the threads of the old probe must be lubricated with this lubricant (Opel № 19 48 602).
- Warm up the engine. The lambda probe must only be removed when the engine is warm.
- Disconnect the lambda probe connector in the engine compartment. The connector is located in the mount on the gearbox.
- Unscrew the lambda probe from the exhaust manifold.
- Protect your hands from burns (work gloves, cloth).
- When mounting, tighten the probe to 30 Nm.
Visitor comments